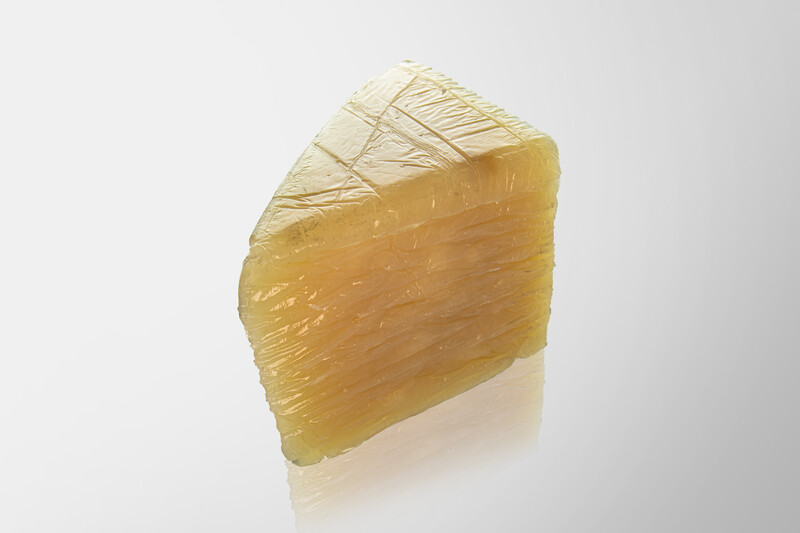
JÄGER Business Blog
WHITEPAPER
Find out which factors influence your SOP!
A secure supply of raw materials and intermediates is an important success factor for any manufacturing company. Whether this is successful depends above all on how well the organization cooperates with its suppliers. The closer both sides are networked, the more effective the cooperation. Especially in the current pandemic situation, supplier integration is therefore a major issue.
Involving suppliers in research and development has several advantages. For example, the company can ensure that all components of its products are designed for production. This is particularly relevant for rubber and plastic parts, as only a few designers have experience in this area.
In practice, there are various approaches to integration, depending on the planning horizon of product development:
Early contact is usually preferable for both sides, as crisis situations with tight deadlines can thus be avoided. Unfortunately, some manufacturing companies still underestimate the complexity of rubber and plastic parts and contact their suppliers too late.
Probably the most common procedural integration in the purchasing of rubber and plastic components is the use of framework agreements. Here, the supplier agrees to provide the customer with an agreed quantity of goods at the agreed conditions over a certain period of time. In practice, there are two options for implementing framework agreements:
In logistics, supplier integration is primarily aimed at reducing frictional losses so that materials and components arrive more quickly where they are needed. One important starting point is order picking. If the supplier delivers goods in packaging units that correspond to the customer’s planned consumption over a certain period of time, there is no need for the customer to decant and sort. This not only reduces the time spent by warehouse personnel, but also the amount of packaging waste.
For example, if the supplier knows how much material the customer will consume for an average production order, he can pre-pack the corresponding quantities of items and fill them into small load carriers, such as those used on the customer’s factory floor. The latter can take the boxes directly from the delivered pallet and process them further. The intermediate steps of decanting and sorting are eliminated.
As far as elastomer components are concerned, production companies should be aware that rubber compounds have a limited shelf life. After about four weeks, the material starts to overage and loses some of its properties. In addition, there is a risk of pre-vulcanization if temperature specifications are not met during transport.
As a result, rubber supply chains are somewhat more fragile than is the case with other materials. On-time deliveries are all the more important in these industries because they cannot keep a buffer in stock for the long term. If there are delivery problems with individual components of a rubber compound, the delivery dates of the finished component are quickly put in jeopardy. This can even affect several suppliers if the component is rare and only a few suppliers have it in their range. It therefore makes sense for production companies to maintain redundancies in their supply chain and, in case of doubt, to release several rubber compounds so that they can react more flexibly to disruptions.
Whitepaper: Secure the Start of Production
Learn which factors influence your SOP!
Share this post!
Jäger Gummi und Kunststoff GmbH
Lohweg 1
30559 Hannover
Tel. +49 511 – 53580
Fax +49 511 – 553394
info@jaeger-gk.de
Management:
Dr.-Ing. Andreas Jäger und
Julius Jäger
Hanover Register Court HRB 59798
DE 813 314 161