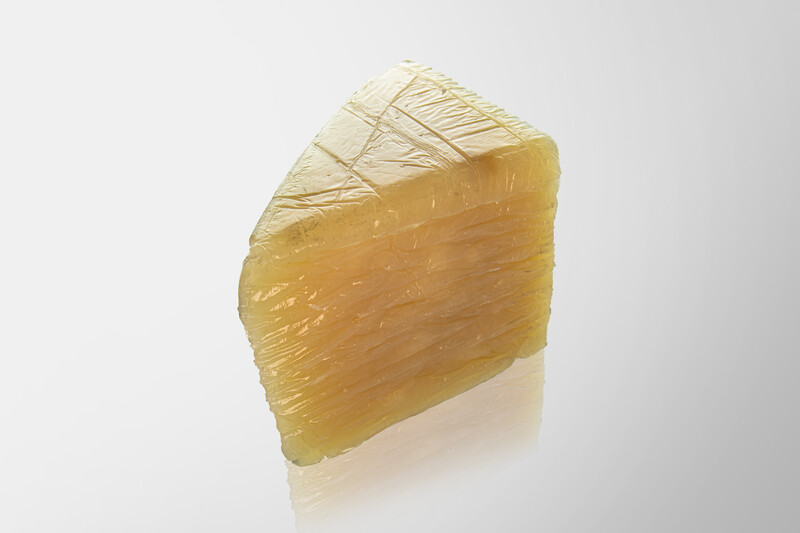
Technical article
WHITEPAPER
Find out which factors influence your SOP!
In design, optimization potentials arise mainly from a flexible, production-oriented design of the components as well as the product itself. One challenge here is that designers often come from the metal sector and align their focus accordingly. Since they have only limited knowledge of elastomers and plastics, they concentrate on optimizing the metal design, their core competence. Overcoming this circumstance is the first challenge in optimizing rubber and plastic components in design.
There is great potential for optimization in material selection and, related to this, in product design. It often makes sense to put the material used for a molded part to the test and critically examine whether an alternative material might not better meet the requirements. On the one hand, materials management is constantly evolving, and on the other, companies sometimes make decisions when developing a new component that turn out to be wrong in retrospect. In both cases, it is worth questioning the choice of material and, if necessary, changing the material.
It often also makes sense to rethink the design of a component in parallel. Material selection and product design go hand in hand. In some scenarios, for example, it is possible to reduce the weight of a component through a design change that provides for less material while using a more robust plastic. Material costs, the service life of the molded part or its carbon footprint can also be significantly improved by such changes.
Some time ago, a customer approached us with the order to optimize the pressure rollers of his conveyor belts. These were relatively energy-intensive and costly to manufacture. Our technical experts replaced the part with a core made of lighter polypropylene encased in a vulcanized rubber component. This reduced manufacturing costs as well as material and energy consumption. You can read the details in our Case Study.
Companies that manufacture multiple products or product lines should consider standardizing their rubber and plastic components. This way, they can supply their entire line with the same molded parts instead of having to keep starting new development projects. This platform design is commonplace in the automotive industry, but other industries can benefit as well.
On the one hand, the modular design of rubber and plastic molded parts lowers development costs because the design department can more easily use standard components and purchasing can realize economies of scale by ordering larger quantities of uniform items. On the other hand, development times are reduced because the design of corresponding rubber or plastic parts is no longer necessary.
In order to exploit the potential described here, material expertise in the field of rubber and plastics is required. Companies that lack this knowledge should therefore work together with a specialist development partner as early as possible and involve the latter's experts in the development team right from the start. This makes it easier to design components correctly right from the start. Experience shows that the earlier this partner receives all the relevant information in the form of a specification sheet, the more efficient the development project will be.
The second major optimization block concerns the production processes, i.e. everything that happens after the raw material is purchased and before it is shipped from the logistics center. The main aim here is to reduce throughput times, downtimes, the reject rate and the use of resources. The most important levers are production planning and tool design.
In contrast to the other optimization areas, process technology is almost exclusively the domain of the rubber or plastics supplier. Customers have relatively little influence on the actual production of molded parts. If they nevertheless want to realize optimization potential in this area, they must take care to select suppliers who demonstrate the appropriate competencies.
A prerequisite for all optimization measures in process technology is a thorough analysis of the articles to be manufactured and the general conditions with regard to production on the customer side. This includes the following questions:
There is great potential for improvement in the creation of mold concepts. Whether rubber or plastic, injection molds are precision tools whose geometry must match the design specifications exactly. Even the smallest deviations from these specifications can jeopardize the functionality of the component. Accordingly, detailed preparation and experience are needed to effectively rule out errors that jeopardize on-time project completion.
In elastomer and plastics production, toolmaking is a major project-internal construction site that includes all process steps common in production and requires, among other things, concepts for design, manufacturing, and transport. This complex process cannot simply be shortened or accelerated. Instead, companies should allow sufficient time for mold construction.
Protecfire, a fire protection specialist based in Luebeck, Germany, approached Jäger with an inquiry for an extinguishing system to fight engine fires in buses. The requirement was for a rubber bladder that would press extinguishing liquid into the lines in an emergency. Jäger developed a corresponding elastomer component for the customer and created a mold concept that guarantees reliable core centering and thus high quality. More details about this project can be found in our Case Study.
The production time of injection molded parts depends, among other things, on how quickly the raw mass is distributed within the mold. The speed of distribution, in turn, depends on the design of the mold, in particular the number of cavities. The more cavities there are, the more raw material can be injected into the molds at the same time and the less material has to be distributed via channels. At the same time, sprue-related material losses decrease, since less rubber or plastic remains in the channels.
However, as the number of cavities increases, so does the size of the mold, which increases its cost. At the same time, the mold must also fit into the injection molding machine and cannot be arbitrarily large. Both factors must be carefully considered. Building a larger mold is not always the best solution.
Material that remains in the channels of the mold after the molded parts are finished must either be recycled or disposed of. This increases unit costs, especially in the production of rubber components, because the vulcanization process is irreversible. For this reason, reducing sprue losses is an important optimization approach in process technology.
In particular, hot and cold runner technology should be mentioned at this point. Both temper the sprue system separately and thus prevent the material from hardening prematurely. In the case of plastics processing, the channels are heated so that the compound first solidifies in the molds. In the case of elastomer products, on the other hand, the channels are cooled.
Downtimes are always a problem in production, because if a machine or system is not running, it does not generate any profit. Therefore, it is also important to optimize downtimes in the rubber and plastics sector.
The primary control levers for this in the injection molding process are the temperature, the injection pressure and the cooling or heating duration of the mold, which in turn influences the cycle times. Added to this are the selection of the appropriate material and intelligent mold design. The lack of customer influence is particularly noticeable in these areas. Therefore, when looking for suppliers, companies should make sure to choose production partners who have the appropriate competencies.
The challenge in material selection is to find a material mix that is best suited to the intended use of the product. This not only has a positive effect on the quality of the product being developed. Smart material selection decisions can help reduce the overall cost of the product (e.g., by reducing material usage) and improve the company’s carbon footprint (e.g., by reducing process-related waste). Wrong decisions, on the other hand, deteriorate the functionality and reliability of the component – and thus of the machine or plant.
Key success factors in selecting the right material are expertise and experience. Companies achieve the best results when they integrate material experts into their development team right from the start. This not only enables fast, targeted selection of the right plastic or rubber compound, but also close integration of compound development, compound production and analysis of physical properties. The number of development cycles can thus be kept to a minimum.
Companies that use specially manufactured material compounds for their rubber and plastic components often suffer from high purchase prices. The reason for this is that the material suppliers’ kneading machines require a minimum quantity of raw materials to operate. This is usually also the contractual minimum purchase quantity for the customer. In the case of special mixes, it is simply not possible to purchase according to demand. For example, if the supplier produces five tons, the customer must also purchase five tons, even if he only needs one ton. Otherwise, the supplier would not get rid of the remaining four tons, because they are individually adapted to the specific requirements of a company.
The situation is different when companies order standard blends. There are so many customers for these that individual customers can also order smaller quantities than the capacity of a vat. This means that orders can be placed in line with demand.
When it comes to material selection, two extremes can often be observed. Some companies focus on price and choose a material that is as inexpensive as possible. Others opt for the premium option and use a material that far exceeds their requirements. Both can have negative consequences.
Minimizing the price often results in the rubber or plastic component being of low quality and having to be replaced frequently. This results in follow-up costs that quickly put the low purchase price into perspective and lead to undesirable delays. In addition, there is a risk that cheap parts will have a negative impact on the company’s carbon footprint from a process and material perspective.
The other extreme, the unnecessary selection of premium materials, increases production costs without offering any real countervalue. In some cases, the increased properties do not even play a role for the end product. “A lot helps a lot” is not always the right solution in the rubber and plastics sector.
It is better to tailor the material precisely to the requirements of the application scenario. Outliers in the direction of price or practical characteristics are rarely helpful.
Supply problems in the material area often have an impact on the entire value chain, as the lack of individual components affects the manufacture of other products. Companies whose rubber and plastic components are regularly unavailable should therefore consider switching materials. There are often alternative materials that have comparable properties and are significantly easier to procure.
It is also worth keeping an eye on the raw materials markets. Supply problems of certain materials are often the result of foreseeable developments. Those who recognize these can take countermeasures at an early stage. If in doubt, it makes sense to seek exchanges with rubber or plastics producers who know the market better.
When developing a new molded part, the selection of the material is one of the fundamental steps. Particularly when it comes to compounds that are developed specifically for a product or component, companies must calculate a corresponding lead time for this, because the compound must be tested extensively in the laboratory with regard to its properties. This process takes time, which must be planned in good time to avoid delays in the product development process.
Redundancy is an important optimization factor in supply chain management. If you source all your rubber and plastic components from one supplier, you create an artificial bottleneck, whose failure can have serious consequences. It is therefore advisable to build up a strategic supplier network in order to be able to switch quickly to another supplier if necessary. It should also be borne in mind that some rubber and plastics producers have their own supplier networks and therefore have a certain basic redundancy. It is therefore not absolutely necessary for the customer to coordinate all suppliers himself. Moreover, in this case, the terms of the partnership can be laid down in framework agreements to provide additional security.
Industrial companies bear a great responsibility in the implementation of national and global sustainability goals. This results in numerous obligations, but also opportunities to better position one’s own organization for the future. This is illustrated again and again by the example of components made of rubber and plastic. Their production is fundamentally energy-intensive, however, depending on the scenario, there are opportunities to reduce energy consumption and pollutant emissions to the bare minimum when designing products and processes. The decisive factor in this context is a sensible triad of
About 96 percent of Jäger Gummi und Kunststoff's suppliers are based within the European Union, 80 percent of them in Germany. These suppliers are specifically selected on the basis of their certification according to the environmental standard DIN EN ISO 14001 and (ideally) DIN EN 50001. Companies that want to make their procurement sustainable therefore have ideal conditions open to them.
Whitepaper: Secure the Start of Production
Learn which factors influence your SOP!
Share this post!
Jäger Gummi und Kunststoff GmbH
Lohweg 1
30559 Hannover
Tel. +49 511 – 53580
Fax +49 511 – 553394
info@jaeger-gk.de
Management:
Dr.-Ing. Andreas Jäger und
Julius Jäger
Hanover Register Court HRB 59798
DE 813 314 161