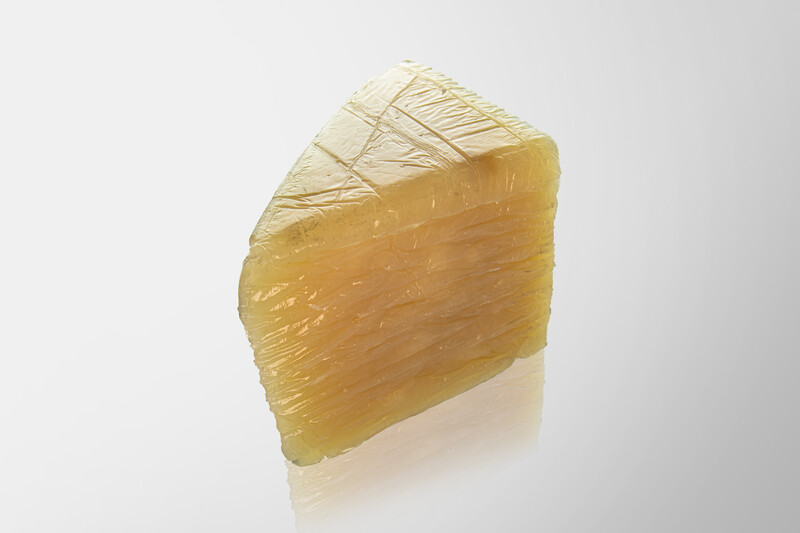
JÄGER Business Blog
what is important?
WHITEPAPER
Find out which factors influence your SOP!
Whenever plastics and elastomers come into contact with food, strict regulations apply to avoid health risks or injury hazards for consumers. This poses challenges for companies, who must take special care in design and material selection. The following article is an overview of the most important aspects that are relevant in the context of food safety.
A major risk is that the materials used contaminate the medium. There are two cases to consider here.
First, coarse particles large enough to cause injuries to the throat and pharynx (for example, plastic splinters) can detach. This is mainly caused by abrasive stresses, for example when the medium rubs against a sharp edge and wears it away over time. However, improper treatment of the material can also cause particles to become dislodged. For example, some types of plastic become porous when permanently exposed to UV radiation.
On the other hand, there is a risk of contamination by microparticles. Although these do not pose a risk of injury, many materials can cause symptoms of poisoning if they enter the human organism. Here, too, abrasion can be the cause, when minute particles are abraded from a component. But chemical reactions can also cause a rubber or plastic part to release ingredients into food, triggered for example by high temperatures or contact with certain media.
Another risk is contamination of the medium by deposits. If, for example, residues accumulate in cracks in the tank during the processing of fresh milk, they will spoil over time and contaminate the remaining goods. Deposits that are harmful to health are often caused by errors during cleaning. In some cases, however, they are also design-related, caused by hollow or dead spaces that are difficult to clean.
Contaminated food is not only risky for consumers. They can also have serious consequences for the manufacturer. These range from costly recalls and loss of reputation to lawsuits by authorities, consumer protection associations or individuals.
Companies operating in the food sector must take special care during production. This applies to the entire manufacturing process, from development to quality control. When dealing with plastics and elastomers, two aspects are particularly relevant: material selection and design.
When selecting materials, it is particularly important to avoid materials that are harmful to health. Materials that are susceptible to abrasive stress are unsuitable in food processing, too. However, requirements of this kind are relatively easy to take into account, since they are included in legal specifications and regulations anyway. Plastics and elastomers used in the food industry must have a number of certifications (including FDA approval and EU standard 10/2011) that exclude certain types of material from the outset.
Yoghurt bottling
It is also important to keep in mind the cleaning of a rubber or plastic component. During cleaning, these parts are often exposed to environmental factors that differ significantly from their primary application. For example, they come into contact with acids, solvents or hot steam. This must be taken into account in the course of material selection. Otherwise, there is a risk that the component’s properties will change and it will release ingredients into the processed medium.
Not only the medium and the plastic or rubber components should be taken into account when selecting materials, but also all metallic elements of the machine system. These include fittings, piping and tanks. The interaction between metal and plastic must not be neglected, otherwise there is a risk of undesirable side effects.
For quality assurance purposes, it is also advisable to use detectable materials. These are materials that are designed in such a way that they can be easily identified in other materials. These include elastomers, for example, which clearly stand out in color from the processed medium, making it easier to visually identify and sort out contaminated articles. Another example includes plastics that are readily magnetic when metals are added, allowing them to be detected by automated sensors. Detectable materials like these reduce the risk of contaminated goods mistakenly passing through quality control.
In design, the main concern is to avoid weak points where particles can detach and contaminate the media. If possible, nothing should stick out that could break off. Sharp edges are also suboptimal, because they can be ground smooth over time, causing material to detach. The same applies to cavities, dead spaces and sharp corners. Substances can be deposited there that spoil over time and are therefore harmful to health. This effect is exacerbated by the fact that these areas are difficult to clean.
In this context, special attention must be paid to the processing of drinking water, which is strictly regulated in Germany. The requirements are even higher than in the general food sector. The reason for this is the fact that contamination in drinking water is often difficult to detect due to its mass. In addition, the subsequent filtering of contaminants is a challenge, as they usually consist of very small particles (e.g., microplastics).
Couplings with hoses
Purifying drinking water is usually costly and time-consuming. For this reason, protective measures are primarily aimed at preventing contamination – for example, through strict hygiene regulations or stringent specifications for materials that come into contact with water. The basis for this is the statutory Drinking Water Ordinance (TrinkwV) as well as the certification of the German Technical and Scientific Association for Gas and Water (DVGW).
The utmost care is required in the food sector, because errors or malfunctions can have health consequences for people. Therefore, when handling rubber or plastic components, manufacturing companies should take care to obtain the necessary certifications and to comply precisely with all specifications. This applies in particular to material selection, but also to design. Quality assurance is a top priority in the food industry. If you keep that in mind, dealing with plastics and elastomers is no big deal either.
Whitepaper: Secure the Start of Production
Learn which factors influence your SOP!
Share this post!
Jäger Gummi und Kunststoff GmbH
Lohweg 1
30559 Hannover
Tel. +49 511 – 53580
Fax +49 511 – 553394
info@jaeger-gk.de
Management:
Dr.-Ing. Andreas Jäger und
Julius Jäger
Hanover Register Court HRB 59798
DE 813 314 161