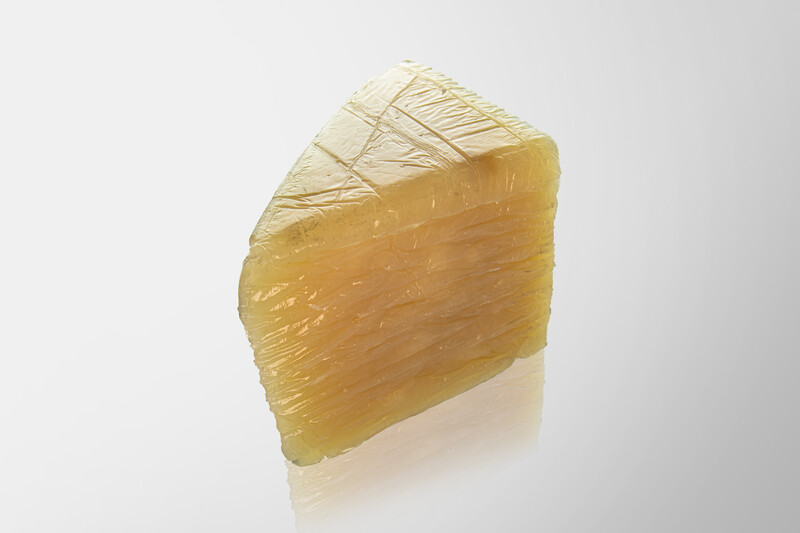
JÄGER Business Blog
WHITEPAPER
Erfahren Sie, welche Faktoren Ihren SOP beeinflussen!
Sowohl in der Elastomer‑, als auch in der Kunststoffproduktion gibt es viele Gründe für Projektverzögerungen. Oft sind Lieferschwierigkeiten entlang der Supply Chain schuld. Gerade zum Start eines Projektes gibt es einen Zeitfaktor, den nur wenige Kunden im Blick haben, obwohl er einen nicht zu vernachlässigenden Teil der Vorlaufzeit vor dem Serienanlauf ausmacht: Der Werkzeugbau. Dieser ist bei Gummi- als auch Kunststoffprodukten wesentlich komplexer, als es den Anschein hat. Wenn Kunden die Herstellung des Werkzeugs während der Entwicklung unterschätzen, bringt dies den termingerechten Projektabschluss in Gefahr.
Die Geometrie des Formteilwerkzeugs muss exakt den Maßen der zu produzierenden Formteile inklusive notwendiger Toleranzen entsprechen. Aus diesem Grund muss für jedes Projekt nach spezieller Kundenzeichnung ein eigenes Werkzeug gefertigt werden, was auch Konstruktion, Fertigung und Transport einschließt. In gewissem Sinne ist der Werkzeugbau ein Projekt im Projekt und das wichtigste Glied entlang der Fertigungskette für ein funktionierendes Teil. Aufgrund des großen Umfangs des Herstellungsprozesses liegt es auf der Hand, dass er häufig Verzögerungen nach sich zieht.
Es gibt vier wesentliche Einflussfaktoren, die häufig die termingerechte Lieferung des Werkzeugs (und damit auch den Produktionsstart des Formteils) hinauszögern:
In der Regel erstellen Kunden eine Konstruktionszeichnung des benötigten Formteils, bevor sie sich an einen Produktionspartner wie Jäger – Gummi und Kunststoff wenden. Diese Zeichnung ist jedoch häufig auf die geometrischen Anforderungen der fertigen Komponente ausgerichtet, nicht auf ihre Produktion. Das führt dazu, dass Kundenvorgaben oft nicht fertigungsgerecht konstruiert sind.
In der Regel erstellen Kunden eine Konstruktionszeichnung des benötigten Formteils, bevor sie sich an einen Produktionspartner wie Jäger – Gummi und Kunststoff wenden. Diese Zeichnung ist jedoch häufig auf die geometrischen Anforderungen der fertigen Komponente ausgerichtet, nicht auf ihre Produktion. Das führt dazu, dass Kundenvorgaben oft nicht fertigungsgerecht konstruiert sind.
Ein Beispiel hierfür ist das unterschiedliche Fließverhalten von Gummi und Kunststoff. Gummi wird kalt in die Form gespritzt und anschließend erhitzt bzw. vulkanisiert, während Kunststoff heiß eingespritzt wird und in der Form abkühlt/erstarrt. In beiden Fällen verhält sich die Rohmischung während der Fertigung grundsätzlich unterschiedlich. Jedoch sind die Feinheiten innerhalb der verwendeten Materialien zu finden. Jedes Material – unabhängig ob Kunststoff oder Gummi – fließt im Spritzprozess unterschiedlich. Hier ist Knowhow essentiell, um die Art und Weise der Anspritzung zu wählen, da es ansonsten zu verschiedenen Fehlern im Material des Endprodukts kommen kann, bspw. sichtbare Fließfehler.
Um zu verhindern, dass Konstruktionsfehler die Fertigung der Formteile beeinträchtigen, überprüft der Produzent zunächst sämtliche Spezifikationen und erstellt ein realistisches Werkzeugkonzept, welches danach mit dem Kunden abgestimmt wird. Dieser Prozess nimmt jedoch Zeit in Anspruch. Sorgfalt ist an dieser Stelle oberstes Gebot, denn auch wenn Werkzeuge im Nachhinein noch nachgearbeitet werden, ist diese Extraschleife zu dringend zu vermeiden.
Nur wenige Produzenten fertigen Werkzeuge heutzutage noch inhouse. Stattdessen lagern sie Aufgaben jenseits der eigenen Kernkompetenzen in der Regel an Dienstleister aus. So auch im Werkzeugbau. In der Regel sitzen die Fertigungspartner innerhalb Deutschlands. Die Zusammenarbeit mit inländischen Dienstleistern vereinfacht die Kommunikation und reduziert den Organisationsaufwand, der sich durch unterschiedliche rechtliche Rahmenbedingungen und Logistikanforderungen ergibt.
In manchen Projekten ist der Kostendruck seitens des Auftraggebers jedoch sehr hoch. Dann ergibt es Sinn, den Werkzeugbau in Niedriglohnländer auszulagern. Die Wahl fällt hierbei oft auf China, da hier eine robuste Stahlindustrie zur Verfügung steht und die Rohstoffkosten geringer sind.
Die Qualität des Werkzeugs ist durchaus mit deutschen Fabrikanten vergleichbar. Allerdings ist der Koordinationsaufwand entsprechend höher. Insbesondere wenn der Formteilproduzent keine eigene Niederlassung vor Ort hat und die Kommunikation über verschiedene Zeitzonen erfolgt. Zwar beeinträchtigt auch die Koordination mit deutschen Partnern den Zeitablauf des Fertigungsprojekts, im internationalen Kontext bei komplizierten Projekten ist diese Verzögerung allerdings deutlich höher.
Ein weiterer Faktor ist die Logistik. Wird das Werkzeug von einem externen Partner hergestellt, kann der Transport je nach Situation zu Verzögerungen führen. Auch hier kommt es darauf an, ob der Formteilproduzent mit einem lokalen oder einem internationalen Werkzeugbauer zusammenarbeitet.
Wird das Werkzeug in Deutschland oder einem angrenzenden EU-Land gefertigt, nimmt der Transport meist relativ wenig Zeit in Anspruch und kann oft durch eigene Kapazitäten erfolgen. Allerdings können in manchen Fällen wetter- oder verkehrsbedingte Verzögerungen auftreten. Wenn der Werkzeugbauer in Asien fertigt, sieht die Sache anders aus. Dann kann der Transport unter Umständen viel Zeit kosten. Das Werkzeug per Luftfracht zu transportieren geht relativ schnell, ist aber nicht immer möglich. Gerade wenn ein hoher Kostendruck herrscht, weichen viele Unternehmen auf günstigere Transportwege, wie Seefracht oder Schienenverkehr, aus. Entsprechend länger ist auch die Lieferzeit.
Werkzeuge für die Formteilproduktion sind Präzisionsinstrumente. Schon geringes Abweichen von den Konstruktionsvorgaben, insbesondere bei engen Toleranzen, kann die produzierten Artikel unbrauchbar machen. Aus diesem Grund wird das Werkzeug vor dem Produktionsstart eingehend überprüft.
An dieser Aufgabe sind mehrere Parteien beteiligt. Zunächst überprüft der Werkzeugbauer selbst, ober er alle Spezifikationen korrekt umgesetzt hat. Dann misst der Gummiproduzent noch einmal spezifische Maße nach, bevor er das Werkzeug in die Fertigungsanlage installiert und auf die Spritzgussmaschine einstellt. Der Auftraggeber des Formteils ist in diesen Prozess zwar nicht unmittelbar involviert. Allerdings überprüft er die Korrektheit des Werkzeuges indirekt, indem er die damit gefertigten Muster begutachtet und den Erstmusterprüfbericht überprüft.
Speziell Messungen nehmen Zeit in Anspruch, denn diese müssen sehr präzise sein. Meist kommen hierfür Spezialinstrumente zum Einsatz, die kleinste Ungenauigkeiten identifizieren können.
Der Werkzeugbau ist fester Bestandteil jedes Spritzguss-Fertigungsprojekts, egal ob Gummi oder Kunststoff. Dass eine Spritzgussform benötigt wird, ist den meisten Kunden bekannt. Sie unterschätzen jedoch, wie viel Aufwand hinter der Herstellung steckt. Eine Spritzgussform ist keine Standardkomponente, sondern ein Präzisionswerkzeug, das für jeden Auftrag individuell angefertigt wird.
Die Werkzeugherstellung ist ein Projekt im Projekt. Sie durchläuft den gleichen Prozess wie jede andere Produktion auch, von der Fertigung bis hin zur Freigabe. Das alles kostet Zeit. Der Bau eines Werkzeuges kann weder verkürzt noch beschleunigt werden. Daher ist es wichtig, ihn bereits zu Beginn in der zeitlichen Projektplanung zu berücksichtigen.
Im besten Fall kontaktieren Unternehmen schon während der Entwicklung einen Gummifertiger, der sich mit dem Material auskennt und Erfahrungswerte beisteuern kann. Dadurch wird die Zeitplanung deutlich robuster und potentielle Probleme/Fehler minimiert.
Whitepaper: Den Start of Production sichern
Henning Schröer hat M. Sc. Wirtschaftsingenieurwesen an der Leibniz Universität Hannover mit dem Schwerpunkt Produktionstechnik studiert. Er ist seit 2019 bei Jäger als Vertriebsingenieur für den Standort Hannover tätig.
Jetzt Beitrag teilen!
Jäger Gummi und Kunststoff GmbH
Lohweg 1
30559 Hannover
Tel. +49 511 – 53580
Fax +49 511 – 553394
info@jaeger-gk.de
Geschäftsführung:
Dr.-Ing. Andreas Jäger und
Julius Jäger
Registergericht Hannover HRB 59798
DE 813 314 161